55 Expertentipps und Best Practices zur Lagerkommissionierung
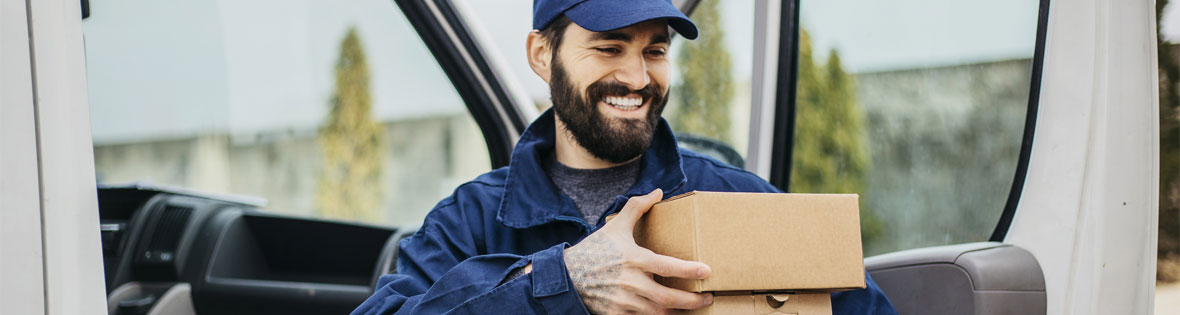
Es gibt viele eingehende und ausgehende Prozesse, die mit der Bewegung und Verwaltung von Lagerbeständen verbunden sind, die die Disziplin der Lagerverwaltung ausmachen. Unternehmen konzentrieren sich oft auf ausgehende Prozesse, um die Kundenzufriedenheit zu erhöhen und betriebliche Ineffizienzen und Kosten zu reduzieren.
Aber die Kommissionierung ist ein entscheidender Teil des Warenausgangs in der Lagerverwaltung. Es umfasst alle Schritte, die beim physischen Abrufen der im Lager gelagerten Artikel zur Erfüllung einer Kundenbestellung erforderlich sind.
Bedeutung der Verbesserung der Kommissionierung im Lager
Intelligente Unternehmen versuchen aus gutem Grund, die Kommissionierung zu verbessern – es ist die arbeitsintensivste und teuerste Aktivität im Lager. in der Regel mehr als die Hälfte der Betriebskosten des Lagers ausmacht.
Verbesserungen bei der Kommissionierung helfen Unternehmen, die richtigen Produkte schneller an die Kunden zu bringen, und geben Sie weniger Geld für die zugehörigen Schritte aus. Lagerauftragswähler nehmen normalerweise eine Kommissionierliste und fahren zu verschiedenen Stellen im Lager, um die Artikel zu holen. suche sie in den Lagerregalen, Extrahieren Sie sie und gleichen Sie den Papierkram ab, um die Genauigkeit der Bestellung vor dem Versand zu gewährleisten.
Der zeitaufwendigste Teil des Kommissionierprozesses ist das Reisen, die 55 % der Zeit des Lagerauswahlhelfers in Anspruch nimmt, im Durchschnitt, gefolgt von Papierkram und anderen Tätigkeiten (20%), Suchen (15%) und Extrahieren (10%), nach einer Studie des Georgia Tech Supply Chain and Logistics Institute. Aus diesem Grund, Viele Arbeiten zur Verbesserung der Kommissionierprozesse zielen darauf ab, unproduktive Reisezeiten zu reduzieren.
Um eine erstklassige Kommissionierung zu erreichen, müssen Sie wissen, wo sich die Produkte befinden, genau wie viele verfügbar sind, zu wissen, wie viele Sie benötigen – damit Sie nicht für jede einzelne Bestellung einzeln kommissionieren – und sicherstellen, dass sie strategisch platziert sind, um eine schnelle Kommissionierung und Verarbeitung für den Versand zu ermöglichen.
Wie können Unternehmen also die Kommissionierzeit minimieren und gleichzeitig eine genaue Auftragsabwicklung und die Sicherheit der Mitarbeiter in einem Lager gewährleisten?
55 Tipps und bewährte Methoden zur Kommissionierung im Lager
Da es nicht den einen Weg gibt, um perfekte Bestellungen zu gewährleisten, Es gibt viele Methoden, Tools und Prozesse, die ein Unternehmen einsetzen kann, um die Kommissionierung zu verbessern. Die Kombination von Strategien, Best Practices und Technologien, die Ihr Unternehmen übernehmen sollte, hängen von der Branche ab, Anzahl der verkauften Artikel und Geschwindigkeit, mit der sich das Inventar durch das Lager/die Lager bewegt.
Ein Blick auf die Gestaltung des Lagers und die Kommissionierungsmethoden in seinen vier Wänden hilft einem Unternehmen bei der Auswahl der richtigen Prozesse, Technologien und Ausrüstung zur Verbesserung der Kommissionierung.
Tipps zur Lagergestaltung für die Kommissionierung
Exzellente Kommissionierung beginnt mit der Auswahl des richtigen Lagerdesigns und -flusses für Ihre Geschäftsprozessstrategie.
-
Wählen Sie einen Lagertyp und -fluss aus. Lagerhallen sind normalerweise so konzipiert, dass sie Waren in einem der folgenden Layouts (oder einer Kombination davon) bewegen.
- U-förmige Strömung positioniert die Empfangs- und Versandrampen auf der gleichen Gebäudeseite, und Produkte bewegen sich U-förmig vom Eingang zum Versand. Dieses Design bietet einen gemeinsamen Docking-Platz und ist in der Regel am besten für kleine Gebäude geeignet.
- I-förmiger Fluss Legen Sie den Empfang an einem Ende des Gebäudes und den Versand am anderen Ende des Gebäudes an, damit sich alle Waren in eine Richtung bewegen. Ein I-förmiger Fluss ist gut für Unternehmen mit hohem Volumen, sowie solche, die eine strenge Sicherheitskontrolle der Waren benötigen, die das Lager betreten und verlassen.
- L-förmiger Lagerfluss hat eine eingehende Entladung an einem Ende und ausgehende Sendungen im rechten Winkel zu diesem Bereich. Dies kann das Cross-Docking – wenn Artikel von einem LKW genommen und sofort auf einen anderen verladen werden – einfacher machen. Dies ist gut für Unternehmen, die möglicherweise nie Produkte auf Regalen lagern, Versand von Lagerbeständen kurz nach der Einbringung.
-
Entscheiden Sie, wie das Produkt innerhalb dieses Flusses organisiert ist. Dies könnte ein sogenanntes triadisches Lagerdesign sein, die in drei Zonen unterteilt ist – schnelllebig, mittel- und langsam drehendes Produkt. In Lagern, die dieses Design nicht verwenden, Produkt ist nicht gezont. Viele Lager haben ein Design, bei dem sie einen Abschnitt mit geeigneten Artikeln automatisieren und immer noch Personen an der Kommissionierung der Artikel beteiligt sind. Zu einem gewissen Grad, in dem anderen.
- Platzieren Sie sich am schnellsten bewegende Produkte in der Nähe der Erfüllung, damit sie leicht ausgewählt werden können.
- Lagern Sie Artikel, die oft zusammen verkauft werden, nahe beieinander.
Kommissionierungsmethoden im Lager
Wenn Sie keine Auswahlmethode haben, Sie kommissionieren für jede Bestellung chronologisch ohne Einblick in die anderen Bestellungen in Ihrer Warteschlange – dies führt dazu, dass den ganzen Tag über viel Zeit verschwendet wird, um das Lager zu durchqueren, um denselben Artikel abzurufen.
-
Betriebe mit geringem Auftragsvolumen oder die hochwertige oder schwere Produkte verkaufen, sollten diskrete, individuelle Kommissionierung, Stückkommissionierung oder Picker-to-Part. Dies ist die einfachste Kommissioniermethode, bei dem eine Person die komplette Bestellung kommissioniert, Spaziergang durch das Lager, Ziehen Sie alle notwendigen Gegenstände und fassen Sie sie oft in einem Behälter zusammen.
-
Für Unternehmen, die Bestellungen mit mehreren Artikeln schnell kommissionieren und verpacken müssen und eine hohe Anzahl von SKUs und Kommissionierungen pro Bestellung haben, Wave-Picking ist eine gute Wahl. Die Kommissionierung erfolgt in geplanten Wellen, und alle Zonen werden gleichzeitig ausgewählt. Die Artikel werden nachgelagert sortiert, während sie für einzelne Sendungen vorbereitet werden. Die Kommissionierwelle legt wie Aufträge nach vordefinierten Regeln zusammen und gibt diese zur gemeinsamen Abwicklung frei, damit die Kommissionierer für die gesamte Welle gleichzeitig kommissionieren können.
-
Um die Kommissioniereffizienz zu erhöhen, Die Mitarbeiter können in Chargen kommissionieren, bei denen sie für mehrere Bestellungen – wie zum Beispiel ähnliche Artikel oder Artikel, die sich in ähnlichen Bereichen befinden – in einer Fahrt kommissionieren. Für Unternehmen mit einer geringen Anzahl von Picks pro Bestellung, Batch-Kommissionierung kann die Reisezeit verkürzen. Der Bediener geht ins Lager, kommissioniert die volle Menge an benötigten Artikeln und ordnet diese dann jedem einzelnen Auftrag zu.
-
Für große Lager mit vielen SKUs, Zonenkommissionierung ist oft von Vorteil. Die Stapelkommissionierung kann die Zonenkommissioniermethode umfassen, bei dem ein Selektor mit der Betreuung eines bestimmten Bereichs im Lager beauftragt ist, alle Artikel für ihre Zone besorgen und dann die Bestellung weitergeben. Aus diesem Grund, Zonenkommissionierung wird auch als Pick and Pass bezeichnet. Die Gegenstände können sich bewegen, zum Beispiel, entlang eines Förderbandes, bis alle benötigten Artikel in der Kiste sind.
-
Innovative Unternehmen versuchen personennahe Setups und Sortiersysteme, um die Effizienz des Kommissionierprozesses zu steigern. Die Lagerauswahl bleibt an einem Ort, und die Produkte werden durch ein Förderband zum Auslesegerät gebracht, ein Robotergerät oder eine andere automatisierte Technologie. Stellen Sie sich Good-to-Person als Automatisierung des diskreten Kommissionierprozesses vor.
-
Eine weitere Möglichkeit, die Reisezeit zu verkürzen, ist Pick-to-Box. Pick-to-Box integriert mehr Automatisierung in die Batch-Kommissionierung. Kommissionierbereiche können in Kommissionierstationen organisiert werden, jeweils durch ein Förderband verbunden. Der Selektor füllt die Kiste mit den Produkten, für die er verantwortlich ist und schiebt die Kiste weiter, bis die Bestellung erfüllt ist.
Kommissionierausrüstung und -technologie im Lager
Ein weiterer wichtiger Aspekt der Lagerverwaltung ist Technologie, die die optimale Strategie für die Einrichtung und die Art des Geschäfts unterstützt. Zum Beispiel, ein Unternehmen mit einer geringen Anzahl von SKUs und weniger kommissionierten Linien kann eine individuelle Kommissioniermethode anwenden, und nutzen Sie die Pick-to-Belt-Technologie oder die Kommissionierung von der Palette. Unternehmen mit einer großen Anzahl von SKUs, die große Mengen bewegen, können sich für Batch-Kommissionierung und Voice- oder Pick-to-Light-Technologie entscheiden.
Bei der Überlegung, welche Geräte und Technologien für Ihr Lager geeignet sind:
-
Stimmen Sie die Technologie auf die Anzahl der SKUs und das Volumen ab. Sehen Sie sich die Anzahl der Zeilen, die pro Tag verarbeitet werden, im Vergleich zur Anzahl der Produkte an. Im Allgemeinen, je höher die Anzahl der SKUs und die Anzahl der Zeilen, desto größer ist der Automatisierungsbedarf.
-
Beginnen Sie mit der Implementierung eines Lagerverwaltungssystems (WMS). Selbst die einfachsten Lagervorgänge benötigen eine Form eines Lagerverwaltungssystems. Suchen Sie nach grundlegenden Kommissionierfunktionen, um SKUs und Artikelstandorte zu speichern und zu verfolgen und die Erstellung von Kommissionierlisten aus Kundenaufträgen zu automatisieren. Ein WMS prüft eine Kundenbestellung anhand des verfügbaren Inventars und stellt Anweisungen in Form einer Auswahlliste bereit. Es berücksichtigt das Layout des Lagers, verfügbare Arbeitskräfte und den Standort der Ausrüstung, um die Effizienz zu maximieren und die Genauigkeit bei der Kommissionierung zu gewährleisten.
-
Integrieren Sie eine Form der mobilen Kommissioniertechnologie. Von den grundlegenden mobilen RF-Scannern, auf Technologien, die die Kommissionierung durch Beleuchten von Knöpfen in den Regalen in einem Kommissionierpfad (Pick-to-Light) oder einen mit einem Headset bekleideten Auswahlschalter per Sprache (Pick-to-Voice) leiten, Es gibt viele mobile Technologien, die für eine genaue Kommissionierung unerlässlich sind, Benutzer zum genauen Gang führen, Regal, oder bin im logischsten Pfad. Stellen Sie sicher, dass die am Boden verwendeten Technologien problemlos mit dem WMS kommunizieren können, damit Sie keine unnötige Komplexität verursachen.
-
Stellen Sie sicher, dass das WMS in das ERP-System integriert ist. Die Verfolgung von Bewegungen und Waren im Lager bietet eine Fülle von wertvollen Daten für andere Abteilungen, wie Einkauf oder Kundenservice. Stellen Sie sicher, dass diese anderen Funktionen Zugriff auf dieselben Daten innerhalb der Software haben, die sie für ihre Aufgaben verwenden.
-
Wählen Sie das richtige Materialflusssystem und passen Sie die Systeme an, wenn SKUs und Volumen steigen. Eine Zunahme der SKUs erfordert viel mehr Logistik im Lager. Bei geringen SKUs und geringem Volumen, ein einfaches Fördersystem wie Gabelstapler tun können, aber mit zunehmendem Volumen und zunehmender Komplexität das Geschäft wird mehr Mechanisierung brauchen. Flurförderzeuge sind ein innovativer Raum, der viele innovative Ideen und Technologien nutzt.
-
Berücksichtigen Sie Fortschritte bei der Ausrüstung, um eine Schmalgangkonfiguration zu ermöglichen. Die Optimierung des verfügbaren Platzes im Lager bietet Vorteile über die Lagerhaltung hinaus – sie kann auch dazu beitragen, die Reisezeit im Kommissionierprozess zu reduzieren. Herkömmliche Lagergänge sind 12 bis 14 Fuß breit. Schmale Gänge sind in der Regel 8-10 Fuß lang, aber kann so wenig wie sechs Fuß sein. Kombination der richtigen Technologien und Geräte, Lager können mit schmaleren Gängen Kommissioniergewinne erzielen.
-
Maximieren Sie die Lagerfläche durch die Verwendung der richtigen Ausrüstung. Die Staplertechnik wird ständig verbessert, und es gibt LKWs, die durch enge Gänge und in enge Räume kommen, wie der knickgelenkte Gabelstapler. Amazon nutzt Roboter, die Roomba-Staubsaugern ähneln. Diese Roboter befördern die benötigten Artikel aus den Regalen zum Kommissionierer und schieben sie wieder an enge Stellen, wenn alle Artikel abgerufen sind.
-
Fördertechnik implementieren. Es gibt Dutzende Arten von Fördertechnik, die für eine effizientere Kommissionierung verwendet werden können, sowie die ergonomische Gesundheit der arbeitenden Mitarbeiter.
-
Sehen Sie sich die Fortschritte bei den Sortiertechnologien an. Kombiniert mit Förderern, Sortiertechnologien sorgen für eine Steigerung der Genauigkeit und Effizienz – für kürzere Durchlaufzeiten und mehr Genauigkeit.
-
Finden Sie heraus, welcher Speicher für das Unternehmen der richtige ist, und übersehen Sie nicht die Vorteile automatisierter Technologien. Ein Karussell, zum Beispiel, automatisiert die Kommissionierung durch ein Regal, das sich entlang einer Schiene dreht, um die Artikel zum Kommissionierer zu bringen. Sie können auf die vom Unternehmen gewählte Kommissioniermethode konfiguriert werden.
-
Machen Sie sich mit allen verfügbaren Optionen der automatischen Kommissioniertechnologie vertraut. Einige Unternehmen haben viel Erfolg mit Pick-to-Light- oder Pick-to-Voice-Geräten. Mit Pick-to-Light, Kommissionierer scannen einen Auftragsbarcode und die Menge und der Standort des Artikels leuchten auf. Pick-to-Voice führt den Kommissionierer und gibt eine Bestätigung über ein Headset. Heute, Augmented-Reality-Technologien ermöglichen Fortschritte wie Pick-via-Smart-Brille, die den Standort und die Menge eines Artikels digital über ein tragbares Headset anzeigen. Sie bieten sprachgeführte Anweisungen und die Möglichkeit, direkt mit dem Headset zu scannen, sodass der Mitarbeiter beide Hände verwenden und die Effizienz mit weniger Berührungen maximieren kann.
-
Implementieren Sie intelligente Technologien. IoT-Technologien können dabei helfen, Bestandszählungen in Echtzeit zu liefern, während die Weiterentwicklung von Wearables-Technologien wie Datenbrillen es einfacher macht, den Überblick über die Lagerbewegungen zu behalten und sicherzustellen, dass die richtige Anzahl von Anfang an vorhanden ist. Dies spart dem Kommissionierer Zeit und die Frustration, nach Artikeln zu suchen, die nicht vorhanden sind.
-
Entdecken Sie das Potenzial von Kommissionierrobotern. Picker-Roboter können die Kommissionierung tatsächlich übernehmen, mit der Fähigkeit, hohe Regale zu erreichen und Gegenstände zum Verpacken zu holen, Gleichzeitig sind sie mit Sensoren ausgestattet, die verhindern, dass sie mit Personen oder Regalen zusammenstoßen.
-
Lernen Sie Co-Bots kennen. Co-Bots können nützlich für Aufgaben sein, die sich wiederholen, erfordern aber auch ein gewisses Maß an menschlichem Eingreifen. Der Co-Bot kann die Box zusammenbauen, zum Beispiel, oder holen Sie Gegenstände mit vorhersehbarer Form oder Gewicht – wie zum Beispiel einen Schuhkarton.
Best Practices und Strategien für die Lagerkommissionierung
Das Lagerdesign, Kommissionierungsmethoden und -technologien helfen dabei zu bestimmen, welche der folgenden Strategien zur Verbesserung Ihrer Kommissionierprozesse am sinnvollsten sind.
Beginnen Sie mit einem klaren Ziel, was Sie verbessern möchten und wie Sie es messen werden. Wählen Sie dann die Tipps aus, die am sinnvollsten sind.
-
Fragen Sie die Leute, die im Lager arbeiten, wo die Engpässe sind. Vergessen Sie nicht die vielen Menschen, die Ihre Prozesse oft unterstützen, darunter Bürokaufleute, Gerätebetreiber und andere.
-
Legen Sie die Kommissionierziele nicht auf Durchschnittswerten fest. Saisonalität und wirtschaftliche Trends werden einen großen Einfluss darauf haben, wie Lagerbestände in das Lager ein- und ausgelagert werden. Schau dir die Gipfel und Täler an, wenden Statistiken an und verwenden Algorithmen, um vernünftige Ziele zu bestimmen.
-
Verfolgen Sie die Produktivität der Kommissionierer. Die Kenntnis der Produktivitätsstufen ermöglicht es dem Lagerleiter, die Schichten so zu gestalten, wie die Arbeit am besten aufgeteilt werden kann. Sehen Sie sich die durchschnittlichen Picks pro Personenstunde an, sowie die Umkehrung, durchschnittliche Personenstunden pro Pick. Die durchschnittliche Arbeit pro Auftrag ist dann die durchschnittliche Anzahl der Kommissionierlinien pro Auftrag multipliziert mit den durchschnittlichen Personenstunden pro Kommissionierung.
-
Messen und verbessern Sie die gesamte Auftragszykluszeit oder die interne Auftragszykluszeit. Die Kommissionierung ist ein großer Teil der Berechnung der Gesamtzeit, die für die Bearbeitung einer Bestellung benötigt wird. Die Verfolgung dieser Zahl liefert ein Maß für die Kommissioniereffizienz.
-
Sehen Sie sich die Genauigkeit der Bestandszählung nach Standort an und nehmen Sie Standortfehler (z. B. Fehlbestände/Rückstände) auf. Dies weist darauf hin, dass am angegebenen Standort nicht genügend Menge vorhanden ist.
-
Messen Sie die Ausführungsrate (nach Position und Bestellungen), um die an diesem Tag versandten Artikel mit der Gesamtzahl der an diesem Tag bestellten Artikel zu vergleichen. Die Füllrate ist eine gute Möglichkeit, um sicherzustellen, dass der Lagerbetrieb die Kundennachfrage erfüllt, und wird normalerweise täglich berechnet.
-
Messen Sie die Genauigkeit der Kommissionierung. Die Kommissioniergenauigkeit steht im Benchmarking-Bericht von DC Measures 2020 auf Platz drei der wichtigsten Benchmarks für Lagerhallen. Eine geringe Kommissioniergenauigkeit weist auf die Notwendigkeit effizienterer Prozesse hin, bessere Kontrollstandards, Vertiefung und mehr.
-
Vergessen Sie nicht KPIs, die die Mitarbeiterproduktivität messen. Dazu gehören pro Stunde kommissionierte Versandlinien, abgesetzte Linien pro Direktstunden, abgesetzte Leitungen pro Gesamtstunden des Verteilzentrums (DC), jährliche Gesamt-DC-Stunden/Gesamt-DC-Kosten und DC-Kosten pro Gesamtarbeitsaufwand.
-
Wählen Sie nicht mehr als sechs Benchmarks aus, Targeting-Metriken, die helfen, das Lager effizienter zu verwalten und die Effizienz mehrerer Einrichtungen zu vergleichen.
-
Überprüfen Sie Ihren Lagerraum jedes Mal, wenn Sie Ihre physische Zählung durchführen. Ein schnelldrehendes Konsumgüterlager muss mindestens alle fünf Jahre aktualisiert werden, da sich Produktsortimente und Verbraucherwünsche sowie größere wirtschaftliche Kräfte ändern. Wenn das Design des Lagers nicht weiter entwickelt wird, werden Kommissionierstrategien und -verbesserungen behindert.
-
Üben Sie das Zählen von Zyklen, um SKU-Komplexität und Verschwendung zu vermeiden.
-
Techniken wie die ABC-Bestandsanalyse (von denen es verschiedene Arten gibt) ermöglichen es Unternehmen, SKUs zu ordnen und zu organisieren und Produkte zu entfernen oder zu verschieben, die ihren Betrieb blockieren.
-
Betrachten Sie über das Ranking von SKUs nur nach Dollarvolumen hinaus, sondern auch, wie jede SKU Ressourcen wie Arbeit und Platz verbraucht. Sortieren Sie SKUs nach der Häufigkeit, mit der sie in einem bestimmten Intervall ausgewählt wurden, Rentabilität, oder Schwierigkeiten bei der Herstellung, zum Beispiel.
-
Implementieren Sie einige Lean-Prinzipien. Führen Sie regelmäßige Gemba-Begehungen durch – verbringen Sie Zeit damit, Lagerprozesse zu beobachten und wirklich zu verstehen, wie sie abgeschlossen sind – um Ineffizienzen in der Einrichtung zu identifizieren. Unternehmen können auch Poka-Yolk-Techniken implementieren, wo sie ihre Operationen fehlersicher machen und nach Wegen suchen, um unbeabsichtigte Fehler zu vermeiden. Ein Beispiel hier ist, wie Cross-Docking den Fluss im Lager verbessern kann.
Tipps zur Lagerkommissionierung
Wenn das Lagerpersonal weiß, worauf das Unternehmen seine Anstrengungen konzentrieren wird, Es kann mit der Umsetzung der folgenden Tipps beginnen, um die Effizienz und Genauigkeit zu steigern und die Arbeitssicherheit zu verbessern.
-
Speichern Sie beliebte SKUs zusammen. Pickdichte kann erhöht werden, zumindest lokal, indem Sie die beliebtesten SKUs zusammen speichern. Dann, Kommissionierer können auf kleinem Raum mehr Kommissionierungen vornehmen, Sie reduzieren den Platzbedarf, den sie abdecken müssen, und steigern die Produktivität.
-
Achten Sie genau auf die Produktschlitzung. Slotting bezieht sich auf die sorgfältige Platzierung von Einzelkisten innerhalb des Lagers, so dass ähnliche Arten von Inventar zusammen gespeichert werden. Sie können nach physischer Größe gruppiert werden, oft zusammen bestellte Artikel, Saisonalität und mehr. Durch das richtige Schlitzen des Produkts, Unternehmen können bis zu 30 % Arbeitseinsparungen erzielen und außerdem eine bessere Ergonomie im Lager sicherstellen, Supply Chain Secrets sagt. Slot nach Volumen und Bewegung und überprüfen Sie die Strategie ein- oder zweimal im Jahr. Ein WMS kann bei der Identifizierung der richtigen Slotting-Strategien helfen, und es gibt viele Algorithmen, die hier helfen können.
-
Batch-Einzellinien-Bestellungen. Einzeilige Bestellungen sind Kundenbestellungen für nur einen Artikel. Aus diesem Grund, Sie müssen am Ende eines Kommissionierpfads nicht sortiert werden, und Sie können die Effizienz steigern, indem Sie einen Kommissionierer so viele davon wie möglich auf einer Fahrt abholen lassen.
-
Ausgleichen Sie Lagerauffüllung und Kommissionierung, um sicherzustellen, dass die Artikel da sind. Laut Supply Chain Secrets gilt als Faustregel ein Aufstocker pro fünf Kommissionierer. aber das hängt von den jeweiligen Strömungsmustern ab. Manchmal, Lager machen den Fehler, Produkte nur nach Umsatz zu messen, wenn sie die Bewegung des Produkts betrachten sollten, Berücksichtigung von Volumen und Umsatz.
-
Stellen Sie sicher, dass der richtige Papierkram mit der richtigen Bestellung verbunden ist. Ein Fünftel der Zeit eines Lager-Selektors wird verwendet, um sicherzustellen, dass der Papierkram korrekt ist. pro Georgia Tech. Dies kann durch die Implementierung von RF-Scannern erheblich erleichtert werden. die den Prozess automatisieren und die Genauigkeit sicherstellen, indem sie den Lieferschein für die Bestellung drucken.
-
Strukturieren Sie Picklisten für effizientes Verpacken. Überlegen Sie, wie die Artikel am besten in den Karton passen, in dem sie versendet werden. Ein WMS kann die Kommissionierungen in einer Kommissionierliste sequenzieren, sodass große Artikel zuerst kommissioniert werden. zum Beispiel.
-
Maximieren Sie die Trefferdichte. Eine Möglichkeit, dies zu tun, besteht darin, die Dichte der Picks zu erhöhen, Minimierung des Abstands zwischen den Picks, um die Anzahl der Picks pro Punkt zu erhöhen und damit die Produktivität zu steigern.
-
Mischen Sie nicht mehrere SKUs an denselben Lagerplätzen. Viele Lager haben noch einen Lagerplatz, der nur an eine Regalebene mit bis zu zehn verschiedenen SKUs gebunden ist. Dazu muss der Mitarbeiter mehrere Produkte nach dem richtigen Artikel durchsuchen.
-
Versuchen Sie, Berührungen der Ware zu minimieren. In den meisten Lagern, sieben bis acht Personen vom Wareneingang über den Warenausgang bis zur Lagerverwaltung einen Artikel berühren, aber die Best-in-Class-Unternehmen werden nur drei bis vier Berührungen haben. Eine Möglichkeit, Berührungen zu minimieren, besteht darin, dass Selektoren Artikel auswählen und sie direkt in den Versandkarton legen. keine Plastikbehälter auf einem Wagen.
-
Integrieren Sie Gewichtsmessungen mit WMS. Unternehmen, die große und schwere Artikel versenden, können die Genauigkeit der Kommissionierung erhöhen, indem sie Informationen über das Gewicht des Artikels mit der Kommissionierliste verknüpfen. Wenn die Auswahl lautet, zum Beispiel, eine Einheit zu kurz, Das System benachrichtigt den Arbeiter automatisch, dass das Gewicht zu niedrig ist und weist ihn an, eine weitere Einheit hinzuzufügen.
-
Wählen Sie vom Bodenstapel. Eine Strategie zum Einteilen von Produkten besteht darin, dass der Selektor mithilfe eines Hubwagens oder Hubwagens drehfreudige Artikel aus Kartons auf Paletten auf dem Boden entnehmen kann. Dies kann effizienter sein, als diese schnell verkauften Artikel auf hohen Palettenregalen zu lagern.
-
Die Leute sollten horizontale Karussells anstelle von vertikalen Liften verwenden. Mehrere Benchmarking-Bemühungen im Laufe der Jahre haben gezeigt, dass es mehr kostet, vertikal auszuwählen als horizontal. Aber auch die Lagerauslastung erfordert eine vertikale Lagerung. Lassen Sie die Artikel mit der langsamsten Geschwindigkeit aus dem vertikalen Lager holen und halten Sie Artikel mit hoher Geschwindigkeit auf Bodenniveau.
-
Wählen Sie aus einem Forward- oder Fast-Pick-Bereich. Unternehmen gestalten Bereiche ihres Lagers, um beliebte SKUs zu beherbergen, die sich im Erdgeschoss befinden und durch Lagerbestände aus anderen Bereichen des DC aufgefüllt werden. Georgia Tech sagt, dass der häufigste Forward-Pick-Bereich das Palettenregal im Erdgeschoss ist, das durch Herunterbewegen von Paletten von höheren Ebenen aufgefüllt wird. Andere Beispiele sind ein Karton-Durchlaufregal, das aus dem Massenlager aufgefüllt wurde, oder spezielle Ausrüstung wie ein Karussell oder ein A-Frame, die woanders gelagert werden.
Maßnahmen zur Schulung und Betreuung der im Lager arbeitenden Mitarbeiter sind ein weiterer wichtiger Bestandteil, um eine effiziente, präzise und kostengünstige Kommissionierung.
-
Stellen Sie sicher, dass die Gründe für die Lagerverwaltungsstrategie und ihre Bedeutung für das Geschäft von allen Lagermitarbeitern verstanden werden. nicht nur Manager. Ein großartiges Beispiel dafür, warum dies wichtig ist, kommt von SI Systems, die darauf hinweist, dass, wenn viele Unternehmen die doppelte Barcode-Verifizierung implementieren, wo der Bediener die Produkt-SKU und dann die Palette scannt, Genauigkeit zu verbessern. Jedoch, Stattdessen scannt der Bediener die Palette oft doppelt, weil es schneller ist. Der Mitarbeiter tut dies, weil er die Produktivität oder den Durchsatz erreichen möchte und nicht erkennt, warum das Scannen von beidem für die Bestandsgenauigkeit entscheidend ist. Sie sollten einen formellen Schulungsprozess mit Teammitgliedern durchführen und die geschäftliche Begründung für jeden Teil eines Prozesses erläutern.
-
Verwenden Sie echte Metriken, um realistische Leistungsstandards für Lagermitarbeiter festzulegen. Verwenden Sie Metriken wie kommissionierte Auftragspositionen pro Stunde und Kommissionierungskosten für jede Auftragsposition und versuchen Sie, diese zu verbessern, indem Sie den Selektoren die richtigen Technologien zur Verfügung stellen, die eine höhere Effizienz und Genauigkeit ermöglichen. wie Pick-to-Light und Pick-to-Voice.
-
Zusammenarbeit fördern. Ein Qualitäts-Dashboard oder ein Kontrollzentrum kann helfen, die Gesamtleistung des Lagers zu überwachen, um Teams zu belohnen und zu motivieren. aber achten Sie auch darauf, die Gewinne einzelner Mitarbeiter hervorzuheben. Zeigen Sie Statistiken zu Leistungsträgern an und schaffen Sie Anreize für eine starke Produktivitäts- und Sicherheitsleistung.
-
Arbeiten Sie daran, Überstunden zu reduzieren. Vergleichen Sie die Gesamtstunden mit der Leistung und sehen Sie sich die pro Arbeitsstunde kommissionierten Auftragspositionen an. zum Beispiel, Arbeitseffizienz zu messen. Berücksichtigen Sie die Normalarbeitszeit im Vergleich zu den Überstunden, kommissionierte Linien pro Tag und Kartonanzahl, Stück oder Paletten kommissioniert pro Periode. Vergleichen Sie diesen Zeitraum mit dem Zeitraum. Wenn diese Zahlen niedrig sind, aber Überstunden sind hoch, Finde heraus warum.
-
Ergreifen Sie Maßnahmen, um den Arbeitsplatz sicherer und in Übereinstimmung mit den OSHA-Standards zu machen. Die besten Lagerbetriebe verfügen über formelle Sicherheitstrainingsprogramme und fortlaufende Schulungen. Stellen Sie Produkte in die sogenannte „goldene Zone“, um eine angemessene ergonomische Gesundheit zu gewährleisten. Gänge und Arbeitsbereiche mit Sicherheitsmarkierungen deutlich kennzeichnen und frei von Schmutz und Gefahren halten. Stellen Sie sicher, dass die Lagermitarbeiter jederzeit alle geeignete PSA tragen, einschließlich Schutzhelme, Brillen, Handschuhe, Masken, richtige Uniformen und mehr.
-
Prozesse regelmäßig überprüfen und verfeinern. Wenn sich die Produktstrategien ändern, Stellen Sie sicher, dass die Lagerstrategie dies auch tut. Herausforderungen in der Lieferkette und Bemühungen zur Erhöhung der Belastbarkeit der Lieferkette werden viele der Prinzipien der Just-in-Time-Bestandsverwaltung, die den Lagerbetrieb seit Jahren leiten, in Frage stellen. In vielen Fällen, Es wird mehr Platz benötigt und Lagerbestände können über längere Zeiträume gehalten werden, um für Überspannungen und Engpässe gewappnet zu sein. In der Tat, Die Nachfrage nach Lagerflächen ist hoch – Das Wall Street Journal berichtete, dass die Aktivität von Industrieimmobilien von April bis Mai 2020 um 43 % gestiegen ist. mit Lagerbedarf von mehr als 100, 000 Quadratmeter am stärksten.
Optimieren Sie die Kommissionierung mit Lagerverwaltungssoftware
Stellen Sie sich die Kundenbestellung wie eine Einkaufsliste vor, die der Kommissionierer erfüllen muss. bei jedem Eintrag in der Liste (sogenannte Bestellzeilen) mit Angabe des Artikels und der Menge. Im Idealfall, ein Lagerverwaltungssystem vorhanden ist, um den verfügbaren Bestand zu überprüfen und zu finden, sowie Bestellungen in einer Kommissionierliste neu zu organisieren, die das Layout des Lagers berücksichtigt, um die Geschwindigkeit zu erhöhen. Die Anzahl der Kommissionierlinien kann ein Hinweis darauf sein, wie viel der Arbeiter im Lager herumlaufen muss, um die für die Bestellungen benötigten Artikel zu erhalten.
Unternehmen können sich an Lagerverwaltungssysteme (WMS) wenden, um die Ein- und Ausgangsprozesse ihrer Lager zu verwalten und einen Überblick über alle vorrätigen SKUs und ihren Standort zu erhalten. Die WMS-Funktionalität baut auf der einer Bestandsverwaltungslösung auf, und verfügt auch über Funktionen, die bei der Speicherstrategie und beim Personalmanagement helfen. Das WMS liefert Details zu allen Artikeln im Lager – physische Abmessungen, wie es verpackt ist, wo es gespeichert ist und der effizienteste Weg, um zu ihnen zu gelangen.
Ein WMS unterstützt die Terminplanung, Empfang, Qualitätssicherung, wegräumen, Standortverfolgung, Auftragsverwaltung, Kommissionierung, Verpackung und Konsolidierung und Versand. Das WMS wandelt einen Kundenauftrag in eine Kommissionierliste um und verfolgt die Auftragsmontage. Das WMS kann auch Eingangsprozesse in einem Lager verwalten, zeigt, wo Inventar gelagert werden soll, Verfolgung der Mitarbeiterproduktivität, Sicherstellen, dass Bestellungen Versandpläne einhalten und mehr. Es kann auch an die Auftragsverwaltungs- und ERP-Systeme angebunden werden. Speziell, für die Kommissionierfunktion, ein robustes WMS kann Pick-to-Light unterstützen, HF-gerichtete Operationen, Arbeitsplanung, SKU Slotting und vieles mehr.
Das richtige WMS skaliert, wenn neue Funktionen benötigt werden, und passt sich an sich ändernde Prozesse an. Während das Gebäude selbst statisch bleiben kann, Prozesse und Technologien eines Unternehmens sollten nicht in Stein gemeißelt sein. Indem man sich ständig die Systeme anschaut und wie die Leute sie verwenden, um ihre Arbeit zu erledigen, Lagerverwaltung kann ständig verbessert werden, Mitarbeitern helfen, ihre Arbeit effektiver zu erledigen und sicherzustellen, dass Kunden weiterhin bei Ihrem Unternehmen kaufen und Ihrem Unternehmen vertrauen.
Unternehmen
- 20 Top-E-Commerce-Trends für 2022 und darüber hinaus
- 53 Online-Jobs, die Teenager diesen Sommer ausprobieren können (verdienen Sie mehr als 20 USD pro Stunde!)
- Verteiltes Inventar definiert:Wie es funktioniert und wann es verwendet wird
- Opinion Outpost Review:Der vollständige Leitfaden für 2021 (verdienen Sie mehr als 10 USD/Stunde)
- 47 Online-Geschäftsideen, die Sie diesen Monat starten können
- 49 erfolgreiche Etsy-Shop-Ideen, um ab heute Geld zu verdienen
-
4 Strategien zur Rentenplanung, auf die Sie sich in unsicheren Zeiten stützen können
Bisher, 2020 hat keine Schläge gezogen. Die Coronavirus-Pandemie zwang viele in den USA in Quarantäne. eine Börsenschmelze eingeleitet, verursachte eine weltweite Rezession, und führte dazu, dass Mill...
-
Selbstständigkeit &Medicaid
Die Selbstständigkeit hat ihre Vorteile – Sie sind keinem Chef unterstellt und legen Ihren eigenen Zeitplan fest. Jedoch, Sie haben auch keine Leistungen an Arbeitnehmer, wie 401(k)-Pläne und Gruppenk...
-
Wie schneidet Ihr Privatkredit im Vergleich zum Durchschnitt ab?
Viele oder alle Produkte hier stammen von unseren Partnern, die uns eine Provision zahlen. So verdienen wir Geld. Unsere redaktionelle Integrität stellt jedoch sicher, dass die Meinungen unserer Exper...
-
Ich habe Angst, meinen Job zu verlieren! Wichtige Geldtipps zum Befolgen
In Zeiten wirtschaftlicher Unsicherheit oder aufgrund von Leistungs- oder Arbeitsdynamik, Sie könnten an einen Punkt gelangen, an dem Sie sich Sorgen machen, Ihren Job zu verlieren. Der Verlust des Ar...